April
2002 |
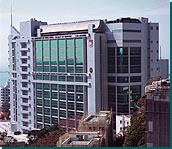 |
|
|
The University of Hong Kong Faculty of Medicine
Advanced
learning
Groundbreaking research
into various areas of the medical field has long made the University
of Hong Kong's
Faculty of Medicine a widely respected institution, not only in
Hong Kong but around the world. Maintaining the quality of its output
is not an easy task, though, particularly in view of the technological
advances of recent years, which have rendered some of its facilities
obsolete. The faculty was well aware of this, but an opportunity
to develop a new and up-to-date facility did not present itself
until recently, when the Northcote College of Education moved to
Tai Po, thus freeing up a 16,900 sq m site conveniently located
just a block away from the Li Shu Fan Building, the existing home
of the faculty; and not far from the university's teaching hospital,
Queen Mary Hospital.
With funds provided by the
University Grants Committee, the Hong Kong Jockey Club and private
donors, Percy Thomas Partnership (HK) Ltd designed the new medical
complex which would consolidate all of HKU's medical facilities
-- i.e. those housed in Li Shu Fan and others scattered over the
campus -- under one roof.
It was a challenging
project: the complex had to be built on a relatively small site
located on a steep slope, and the nature of the building meant that
safety considerations must be paramount in the design.
The two primary functions
of the complex -- research and teaching -- gave rise to a complex
with two connecting but distinctly different blocks. All laboratory
facilities will be accommodated in a 12-storey laboratory block
where advanced medical research will be carried out; while a nine-storey
curvilinear non-laboratory block will house a hi-tech conference
centre, a library, offices and seminar rooms. There will also be
a two-level car park.
According to Percy Thomas
Partnership (HK) managing director Christopher Howe, safety was
a key factor in the planning strategy for the laboratory building.
Functions were zoned according to the level of risks associated
with them, with facilities of a highly hazardous nature assigned
an area at one end of the building and those posing the least risk
at the other. The laboratories were divided into three categories,
with category 1 being low-risk, category 2 being laboratories used
for normal university research; and category 3 being the highest
risk category. A progression from high risk to low risk was followed
in their planning within the laboratory block, with the end assigned
to high-risk functions determined by the building's orientation
and circulation pattern, which also determined the vertical planning
strategy for the building.
The main teaching and
student areas are located on the lower floors while the upper floors
were allocated for clinical research, thus confining most of the
student movement to the lower floors and keeping the laboratory
areas relatively separate. Segregation is further enhanced by the
creation of two separate entrances to the laboratory block leading
to two lift cores, one at each end of the building. One leads directly
to the clinical research centre on the upper floors while the other
provides access to the pre-clinical research centre on the lower
levels.
Laboratories were distributed
on either side of a main axis with a services spine down the middle,
the arrangement being determined by the need to provide individual
extracts for all the fume cupboards and biological safety cabinets.
An extensive network of ducts will draw fumes from the fume cupboards
to a two-storey-high plant room on the roof, where they will be
expelled by ducts shielded by a wind scoop designed to encourage
the exhaust to discharge vertically at a high level under any wind
condition, instead of dispersing at a low level where wind turbulence
will lead to pollution. According to Mr Howe, the comprehensive
laboratory provisions have garnered the project worldwide attention.
The main contractor,
Dragages et Travaux Publics (HK) Ltd, was responsible for co-ordination
of the building's services, including production of the combined
services drawings. According to Mr Jean-Pierre Lefoul, Director
of Building Works for Dragages, ease of maintenance was an important
criterion in the choice and design of equipment. "For example,
the drainage system consists of non-corrosive pipes which are epoxy-coated
on the inside, to minimise ageing and avoid corrosion. The main
electrical and mechanical (E&M) services spine is located outside
the laboratories, each served by its own sub-circuit, so that maintenance
can be carried out without the laboratories being disturbed."
To accommodate all the
building services required, the laboratory block features a floor-to-floor
height of 5 m. Dragages used steel formwork to construct the complex
to achieve a better quality finish. Steel shutters were also better
able to withstand the pressure of concreting 5 m high walls in the
laboratory block, said Mr Lefoul.
With about 20 end-user
departments, flexibility is an important consideration. This was
provided by a modular design based on a 1.5 m grid and the use of
gypsum board partitions which were screwed into place, making them
easy to dismantle and move whenever the layout has to be changed.
The support equipment corridor down the middle ensure that any changes
can be accommodated without extensive alterations.
Because of the highly
sensitive nature of the laboratory work carried out in these rooms,
their finishings must also conform to extremely stringent international
hygiene standards. The walls, for example, were sprayed with a self-sterilising
coating which, unlike ordinary plaster, does not harbour bacteria
and is capable of withstanding aggressive environments. The air-conditioning
system was fitted with special filters while the floor was finished
with a continuous sheet of welded and sealed vinyl membrane.
The international procurement
operation required special attention, said Mr Lefoul. "Materials
for the project, including the specialist laboratory equipment,
had to be purchased from overseas suppliers in many countries. As
any disruption in the delivery schedule would have been disastrous
for the tight construction programme, we had to keep the international
communication lines open 24 hours a day."
With the laboratory block
tucked up against the slope, the rest of the site was opened up
to the view of the East Lamma Channel to the southwest. Taking advantage
of this, the architect designed a semi-circular block with continuous
glass walls on the lower levels where those taking a break from
lectures or conferences can enjoy the sweeping sea view.
There are four lecture
theatres in a semi-circular arrangement reflected by the building's
external design. Depending on the size of the function, they can
be either combined or partitioned to serve separate audiences. The
theatres are equipped with an advanced audio-visual system which
can be hooked up to a network both within the complex and beyond.
It will allow events being carried out in the theatres to be displayed
in the departmental seminar rooms as well as cases being treated
at the Queen Mary Hospital to be shown. Scientists conducting research
overseas will also be able to share their studies with those in
the theatres through an international link-up.
The architect has designed
a building which steps down towards the southeast, creating open
courtyards that let daylight into the interior of the offices. Mr
Howe said energy efficiency was a feature of the design that integrates
architectural and engineering systems whilst providing a safe environment.
Glass with superior thermal performance was selected, to make sure
the external envelope would perform well in this regard.
As a result of road widening
works near the site, some trees were destined to be felled. The
university, however, was keen to save those which could be saved.
Since they could not remain where they were, it meant choosing hardy
ones capable of withstanding the stress of being moved to a new
home.
After an assessment,
botanical specialists from the project team determined that a banyan
tree had the potential to survive. This entailed cutting back its
top to slow its growth, then trimming back its roots an equivalent
amount. Dragages constructed a large steel frame around the roots
of the tree and a 300-tonne crane was used to lift and place it
in a 7 m diameter tree pot formed by sheet piles. It was left to
get used to this new environment for another season before the move
took place. Finally, the 55-tonne banyan was slowly moved a distance
of 80 m to its new location by the main entrance of the medical
complex.
Although the construction
took only 23 months, planning for the over 50,000 sq m complex started
way back in 1995, showing the extent of the challenge presented
by the creation of an advanced medical research facility equipped
to function in the information age. The new complex will be ready
for occupation in March 2002.
The University of Hong
Kong
client
Percy Thomas Partnership
(HK) Ltd
architect
Dragages et Travaux Publics
(HK) Ltd
main contractor
Meinhardt (Hong Kong)
Ltd
structural engineer
Parsons Brinckerhoff Asia
Ltd
e&m engineer
Levett & Bailey
quantity surveyor
|