Esh Construction, Aarsleff Ground Engineering, and Sunderland City Council have worked in collaboration to deliver four significant retaining structures in a geotechnical engineering feat on Phase 3 of the Sunderland Strategic Transport Corridor (SSTC3). In just over 12 months, a soil nail wall formed at a 70-degree angle up to 12m high and 250m in length, a large kingpost retaining wall 250m in length, 85m of contiguous bored pile reinforced concrete retaining wall and a 65m reinforced concrete L-shaped wall supported on CFA piled foundations, have been installed. The £40m SSTC3 project - delivered by Esh Construction’s civil engineering division on behalf of Sunderland City Council - will create a new uninterrupted dual carriageway link to the Northern Spire bridge and the city centre. SSTC3 begins at the southern end of the Northern Spire and continues through the former Pallion Shipyard, underneath the Queen Alexandra Bridge, into Deptford Terrace and onto the city centre.
Aarsleff Ground Engineering was appointed by Esh to undertake the design and geotechnical works package for the significant retaining structures which were necessary to create space for the highway between the former Pallion Shipyard, the upper existing highway, and the Tyne & Wear Metro line. To make the new highway possible, the retaining structures and slope stabilisation works were essential in navigating a height difference of approximately 20m between the bordering land with existing land falling steeply across the site.
King Post Ground Anchors
The king post retaining wall between the north side of the new highway and the former Pallion Shipyard was designed by Capita. It sits directly in front of an old retaining structure which is assumed to have no retaining capacity but had to be incorporated into the scheme. Measuring 250m in length, at 6m centres it is restrained with 2-4 inclined ground anchors depending on the retained height of the new structure. Using precast concrete infill panels, it is constructed against an existing reinforced concrete kingpost wall structure and supported on reinforced concrete pad foundations.
Aarsleff was contracted to design and install over 100 high capacity ground anchors with up to 16 strands, providing working loads in excess of 2,000kN. Standing at 10m high, the king post retaining wall was designed to be a freestanding structure and up to 4 ground anchors were installed at the highest point of the new wall which pinned the old structure and mitigated any associated ground movements. Investigation and trials commenced in August 2019 which tested; the ultimate bond stress at the rock/grout interface of the old quarry, the load transfer behaviour of the proposed anchors, and the ultimate rock/ground bond stresses achievable in the underlying limestone. Anchor loads in excess of 4000kN were successfully proven during these trials and the permanent anchor design for the king post retaining wall was produced.
One year later and installation was underway, which saw 87 ground anchors installed into the newly constructed king post wall – founded on rock from the old quarry – and a further 30 anchors installed into a concrete retaining wall encasing an existing sheet piled counterfort wall founded on CFA piles. Factory manufactured and supplied with a pre-grouted fixed length ready for the installation, the anchors have up to 16 strands and are up to 30m in length. The counterfort wall crosses the backfilled quarry, extending over an area of around two hectares and to a depth of at least 15m. It is an L-shaped section retaining wall of around 5m in height and is built on CFA piles of 750mm diameter, up to 15m deep, and socketed 3m into the competent rock.
The ground anchors were founded into limestone - the depth of which varied greatly over the site – after passing through at least 20m of granular material prior to encountering the limestone. Varied ground conditions on the project resulting in a variety of drilling systems being used to ensure the integrity of the anchors. In addition, each anchor was design checked by the on-site engineer during installation, to ensure they were formed within competent limestone. The top anchors typically have three or four strands each, while those in the bottom rows were 16-strand anchors; installed using a 220mm-diameter casing and 195mm-diameter open bore through the rock. They have a fixed length in the rock of up to 8m.
Up to three rigs were used for the ground anchor installation including two excavator-mounted rigs, one of which sat on top of the wall and installed the top row of anchors and some of the second row down. The second rig, which is capable of installing anchors to a height of about 8.5m, worked from ground level. A collaborative pre-construction design process between Esh Civils, Aarsleff Ground Engineering and Byland Engineering, coupled with agile reactions on site to overcome changes to the ground conditions, allowed Aarsleff to install and test quality ground engineering products safely.
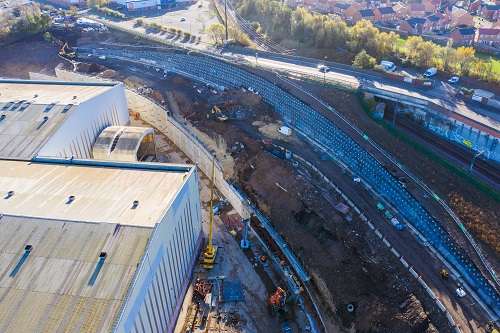
Soil Nails
The largest of the structures under Aarsleff’s scope of works is the soil nail wall which extends across 1,995m2 of wall face between the new highway alignment and the metro line, rising up to 12m high and some 250m long. Formed at a 70-degree angle, it was constructed to retain an existing road embankment and supports a two-lane single carriageway and existing railway. Although originally designed as a drilled steel tube with sheet piles anchored-combi wall, a value engineering activity resulted in the introduction of the soil nail wall faced with gabion stone. The re-design to a soil nail wall solution allowed Esh to provide shared project savings among all parties, de-risked the construction and created something which is more aesthetically pleasing.
Constructing the wall required excavation from the top down in 1.5m-high benches. Senior Geotechnical Consultant, Dr Dan Adams, explains: “The slope was trimmed and cut to the correct profile before the soil nails, which are up to 15m long, were installed along with the structural facing of galvanised steel mesh, which restrains the face of the slope against any movement. The ‘self-drilling’ soil nails are essentially hollow-stem galvanised steel bars with sacrificial drilling bits and bar diameters from 38mm to 51mm. As the bar is drilled into the ground, grout is pumped down the central annulus and into the drilling bit, then it flows back up the drill hole to keep the bore open while the nail is installed. The grout hardens and creates the bond between the nail and the ground.
With the soil nails and mesh installed over the full height of the wall, the non-structural facing of 300mm-thick gabion mattresses were installed, working from the bottom upwards. Filled with a mixture of granular material which will blend with the surrounding terrain, the gabion mattresses will give a softer finish than shotcreting. Excavator-mounted soil nailing equipment was used for the very top benches and, as work progressed down the height of the wall, a working platform was formed where two drilling rigs were placed allowing the installers to work cross-masted. Owing to the sites previous use as a Shipyard, numerous unchartered structures, buried asbestos and existing deep drainage culverts - the ground conditions encountered on the soil nail wall were mixed. The aggressive nature of the ground meant that differential movement and associated settlement needed to be considered and dealt with to provide the required 120-year design life. The soil nail wall is due for completion in March 2021 which will mark the project reaching 80% completion.